Prediction of machining performances in powder mixed electro-discharge machining to process skd61 steel by response surface methodology
Email:
levantao@lqdtu.edu.vn
Từ khóa:
EDM, PMEDM, tungsten compound powder, MRR; TWR
Tóm tắt
In electro-discharge machining (EDM) with mixing powder, it is called powder mixed electro-discharge machining (PMEDM), then machining performances- i.e. material removal rate(MRR) and tool wear rate (TWR) has great significance in evaluating the effectiveness and machining accuracy of the machining method. Therefore, in this study, response surface methodology (RSM) was utilized for estimating functions of process variables {comprising peak current (Ip), pulse on time (Ton), and powder concentration (Cp)} for the machining performances for processing SKD61 steel during EDM process with tungsten compound powder. Box-Behnken matrix was utilized for designing and conducting a series of empirical trials. Analysis of variance (ANOVA) was applied to evaluate the adequate of predictive models. The outcomes reveal that the predicted models of MRR and TWR have a high precision with R2 values of MRR and TWR being 99.2% and 99.11%, respectively. The error comparison of the predictive and empirical values for the confirmed experiments is less than 5%, this once again consolidates that the developed models' accuracy. These development models can efficiently prognosticate the desired machining performances of the PMEDM method for processing SKD61 steelTài liệu tham khảo
[1]. J.T. Philip, J. Mathew, B. Kuriachen, Transition from EDM to PMEDM – Impact of suspended particulates in the dielectric on Ti6Al4V and other distinct material surfaces: A review, Journal of Manufacturing Processes, 64 (2021) 1105–1142. https://doi.org/10.1016/j.jmapro.2021.01.056
[2]. K. Ishfaq, M. Rehman, Y. Wang, Toward the Targeted Material Removal with Optimized Surface Finish During EDM for the Repair Applications in Dies and Molds, Arabian Journal for Science and Engineering, 48 (2023) 2653–2669. https://doi.org/10.1007/s13369-022-07006-x
[3]. R. Singh, R.P. Singh, R. Trehan, State of the art in processing of shape memory alloys with electrical discharge machining: A review, Proceedings of the Institution of Mechanical Engineers, Part B: Journal of Engineering Manufacture, 235 (2021) 333–366. https://doi.org/10.1177/0954405420958771
[4]. S. Srivastava, M. Vishnoi, M.T. Gangadhar, V. Kukshal, An insight on Powder Mixed Electric Discharge Machining: A state of the art review, Proceedings of the Institution of Mechanical Engineers, Part B: Journal of Engineering Manufacture, (2022) 95440542211118. https://doi.org/10.1177/09544054221111896
[5]. A. Erden, S. Bilgin, Role of Impurities in Electric Discharge Machining, in: Proceedings of the Twenty-First International Machine Tool Design and Research Conference, Macmillan Education UK, London, (1981) 345–350. https://doi.org/10.1007/978-1-349-05861-7_45
[6]. K.L. Wu, B.H. Yan, F.Y. Huang, S.C. Chen, Improvement of surface finish on SKD steel using electro-discharge machining with aluminum and surfactant added dielectric, International Journal of Machine Tools and Manufacture, 45 (2005) 1195–1201. https://doi.org/10.1016/j.ijmachtools.2004.12.005
[7]. B. Yan, Y. Lin, F. Huang, C. Wang, Surface Modification of SKD 61 during EDM with Metal Powder in the Dielectric, Materials Transactions, 42 (2001) 2597–2604. https://doi.org/10.2320/matertrans.42.2597
[8]. F.L. Amorim, V.A. Dalcin, P. Soares, L.A. Mendes, Surface modification of tool steel by electrical discharge machining with molybdenum powder mixed in dielectric fluid, International Journal of Advanced Manufacturing Technology, 91 (2017) 341–350. https://doi.org/10.1007/s00170-016-9678-x
[9]. V.T. Le, The role of electrical parameters in adding powder influences the surface properties of SKD61 steel in EDM process, Journal of the Brazilian Society of Mechanical Sciences and Engineering, 43 (2021) 120. https://doi.org/10.1007/s40430-021-02844-6
[10]. V.T. Le, Influence of Processing Parameters on Surface Properties of SKD61 Steel Processed by Powder Mixed Electrical Discharge Machining, Journal of Materials Engineering and Performance, 30 (2021) 3003–3023. https://doi.org/10.1007/s11665-021-05584-9
[11]. V.-T. Le, New insights into the surface features of SKD61 steel at heat-treated and non-heat-treated states as processed by powder-mixed EDM, Materials Letters, 352 (2023) 135199. https://doi.org/10.1016/j.matlet.2023.135199
[12]. https://www.daido.co.jp/en/products/tool/dha_world/index.html.
[13]. A.-C. Wang, L. Tsai, Y.-C. Lin, Characterizing the machining effects of lateral electrodes in electrical discharge machining, International Journal of Precision Engineering and Manufacturing, 15 (2014) 1095–1100. https://doi.org/10.1007/s12541-014-0442-6
[14]. V.T. Le, The influence of additive powder on machinability and surface integrity of SKD61 steel by EDM process, Materials and Manufacturing Processes, 36 (2021) 1084-1098. https://doi.org/10.1080/10426914.2021.1885710
[15]. V.T. Le, L. Hoang, MF. Ghazali, V.T. Le, M.T. Do, T.T. Nguyen, T.S. Vu, Optimization and comparison of machining characteristics of SKD61 steel in powder-mixed EDM process by TOPSIS and desirability approach, The International Journal of Advanced Manufacturing Technology, 130 (2024) 403-424. https://doi.org/10.1007/s00170-023-12680-8
[16]. H.R. Fazli Shahri, R. Mahdavinejad, M. Ashjaee, A. Abdullah, A comparative investigation on temperature distribution in electric discharge machining process through analytical, numerical and experimental methods, International Journal of Machine Tools and Manufacture, 114 (2017) 35–53. https://doi.org/10.1016/j.ijmachtools.2016.12.005
[17]. J. Wang, F. Han, Simulation model of debris and bubble movement in consecutive-pulse discharge of electrical discharge machining, International Journal of Machine Tools and Manufacture, 77 (2014) 56–65. https://doi.org/10.1016/j.ijmachtools.2013.10.007
[18]. K. Furutania, A. Saneto, H. Takezawa, N. Mohri, H. Miyake, Accretion of titanium carbide by electrical discharge machining with powder suspended in working fluid, Precision Engineering, 25 (2001) 138–144. https://doi.org/10.1016/S0141-6359(00)00068-4
[19]. K.. Ho, S.. Newman, State of the art electrical discharge machining (EDM), International Journal of Machine Tools and Manufacture, 43 (2003) 1287–1300. https://doi.org/10.1016/S0890-6955(03)00162-7
[20]. B. Ekmekci, H. Yaşar, N. Ekmekci, A Discharge Separation Model for Powder Mixed Electrical Discharge Machining, Journal of Manufacturing Science and Engineering, 138 (2016) 1–9. https://doi.org/10.1115/1.4033042
[2]. K. Ishfaq, M. Rehman, Y. Wang, Toward the Targeted Material Removal with Optimized Surface Finish During EDM for the Repair Applications in Dies and Molds, Arabian Journal for Science and Engineering, 48 (2023) 2653–2669. https://doi.org/10.1007/s13369-022-07006-x
[3]. R. Singh, R.P. Singh, R. Trehan, State of the art in processing of shape memory alloys with electrical discharge machining: A review, Proceedings of the Institution of Mechanical Engineers, Part B: Journal of Engineering Manufacture, 235 (2021) 333–366. https://doi.org/10.1177/0954405420958771
[4]. S. Srivastava, M. Vishnoi, M.T. Gangadhar, V. Kukshal, An insight on Powder Mixed Electric Discharge Machining: A state of the art review, Proceedings of the Institution of Mechanical Engineers, Part B: Journal of Engineering Manufacture, (2022) 95440542211118. https://doi.org/10.1177/09544054221111896
[5]. A. Erden, S. Bilgin, Role of Impurities in Electric Discharge Machining, in: Proceedings of the Twenty-First International Machine Tool Design and Research Conference, Macmillan Education UK, London, (1981) 345–350. https://doi.org/10.1007/978-1-349-05861-7_45
[6]. K.L. Wu, B.H. Yan, F.Y. Huang, S.C. Chen, Improvement of surface finish on SKD steel using electro-discharge machining with aluminum and surfactant added dielectric, International Journal of Machine Tools and Manufacture, 45 (2005) 1195–1201. https://doi.org/10.1016/j.ijmachtools.2004.12.005
[7]. B. Yan, Y. Lin, F. Huang, C. Wang, Surface Modification of SKD 61 during EDM with Metal Powder in the Dielectric, Materials Transactions, 42 (2001) 2597–2604. https://doi.org/10.2320/matertrans.42.2597
[8]. F.L. Amorim, V.A. Dalcin, P. Soares, L.A. Mendes, Surface modification of tool steel by electrical discharge machining with molybdenum powder mixed in dielectric fluid, International Journal of Advanced Manufacturing Technology, 91 (2017) 341–350. https://doi.org/10.1007/s00170-016-9678-x
[9]. V.T. Le, The role of electrical parameters in adding powder influences the surface properties of SKD61 steel in EDM process, Journal of the Brazilian Society of Mechanical Sciences and Engineering, 43 (2021) 120. https://doi.org/10.1007/s40430-021-02844-6
[10]. V.T. Le, Influence of Processing Parameters on Surface Properties of SKD61 Steel Processed by Powder Mixed Electrical Discharge Machining, Journal of Materials Engineering and Performance, 30 (2021) 3003–3023. https://doi.org/10.1007/s11665-021-05584-9
[11]. V.-T. Le, New insights into the surface features of SKD61 steel at heat-treated and non-heat-treated states as processed by powder-mixed EDM, Materials Letters, 352 (2023) 135199. https://doi.org/10.1016/j.matlet.2023.135199
[12]. https://www.daido.co.jp/en/products/tool/dha_world/index.html.
[13]. A.-C. Wang, L. Tsai, Y.-C. Lin, Characterizing the machining effects of lateral electrodes in electrical discharge machining, International Journal of Precision Engineering and Manufacturing, 15 (2014) 1095–1100. https://doi.org/10.1007/s12541-014-0442-6
[14]. V.T. Le, The influence of additive powder on machinability and surface integrity of SKD61 steel by EDM process, Materials and Manufacturing Processes, 36 (2021) 1084-1098. https://doi.org/10.1080/10426914.2021.1885710
[15]. V.T. Le, L. Hoang, MF. Ghazali, V.T. Le, M.T. Do, T.T. Nguyen, T.S. Vu, Optimization and comparison of machining characteristics of SKD61 steel in powder-mixed EDM process by TOPSIS and desirability approach, The International Journal of Advanced Manufacturing Technology, 130 (2024) 403-424. https://doi.org/10.1007/s00170-023-12680-8
[16]. H.R. Fazli Shahri, R. Mahdavinejad, M. Ashjaee, A. Abdullah, A comparative investigation on temperature distribution in electric discharge machining process through analytical, numerical and experimental methods, International Journal of Machine Tools and Manufacture, 114 (2017) 35–53. https://doi.org/10.1016/j.ijmachtools.2016.12.005
[17]. J. Wang, F. Han, Simulation model of debris and bubble movement in consecutive-pulse discharge of electrical discharge machining, International Journal of Machine Tools and Manufacture, 77 (2014) 56–65. https://doi.org/10.1016/j.ijmachtools.2013.10.007
[18]. K. Furutania, A. Saneto, H. Takezawa, N. Mohri, H. Miyake, Accretion of titanium carbide by electrical discharge machining with powder suspended in working fluid, Precision Engineering, 25 (2001) 138–144. https://doi.org/10.1016/S0141-6359(00)00068-4
[19]. K.. Ho, S.. Newman, State of the art electrical discharge machining (EDM), International Journal of Machine Tools and Manufacture, 43 (2003) 1287–1300. https://doi.org/10.1016/S0890-6955(03)00162-7
[20]. B. Ekmekci, H. Yaşar, N. Ekmekci, A Discharge Separation Model for Powder Mixed Electrical Discharge Machining, Journal of Manufacturing Science and Engineering, 138 (2016) 1–9. https://doi.org/10.1115/1.4033042
Tải xuống
Chưa có dữ liệu thống kê
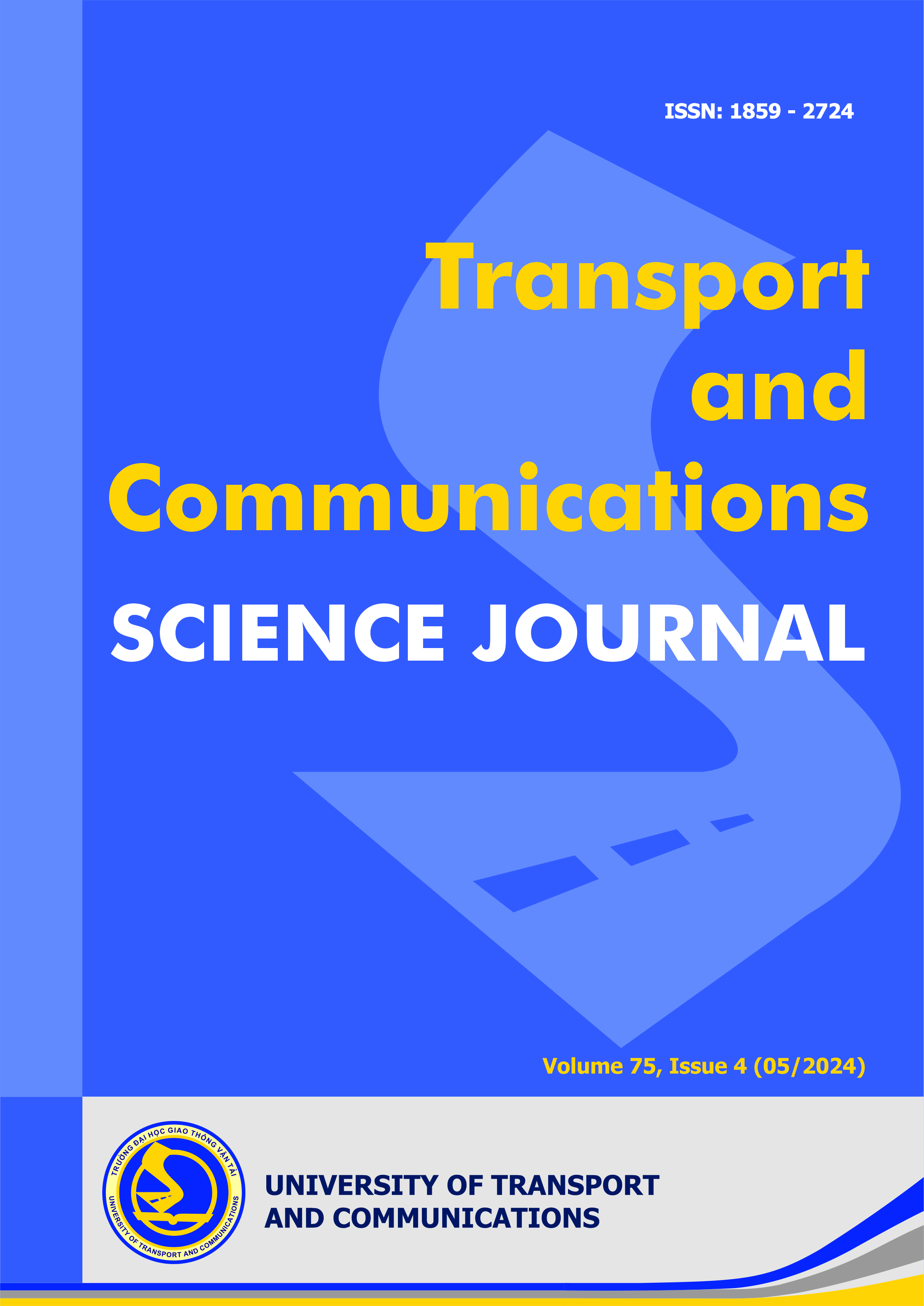
Nhận bài
25/10/2023
Nhận bài sửa
16/01/2023
Chấp nhận đăng
30/01/2024
Xuất bản
15/05/2024
Chuyên mục
Công trình khoa học
Kiểu trích dẫn
Van Tao, L., Tien Long, B., Thi Hong Minh, N., Tien Dung, H., Van Thuc, D., & Hoang Cuong, P. (1715706000). Prediction of machining performances in powder mixed electro-discharge machining to process skd61 steel by response surface methodology. Tạp Chí Khoa Học Giao Thông Vận Tải, 75(4), 1617-1630. https://doi.org/10.47869/tcsj.75.4.12
Số lần xem tóm tắt
203
Số lần xem bài báo
93